|
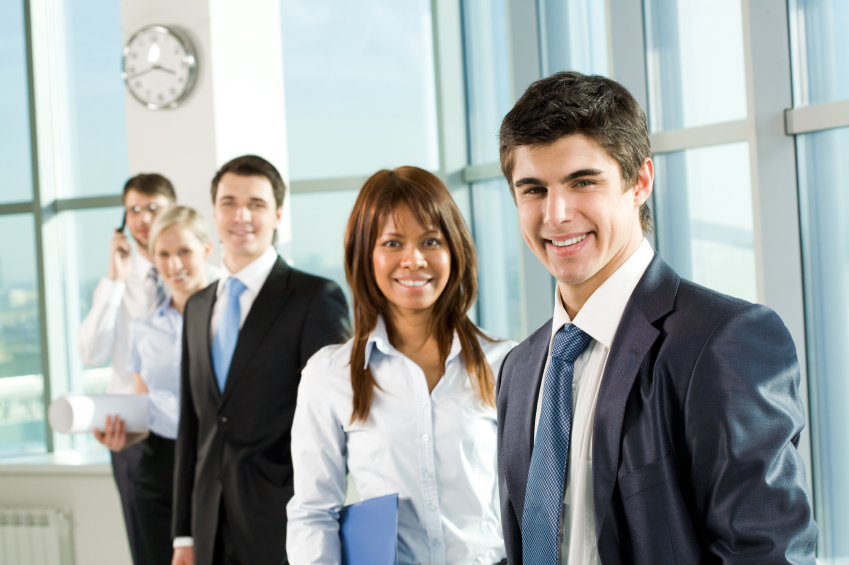 |
BOLIVIA
Bolivia is located in the central zone of South America. With an
area of 1,098,581 square kilometres (424,164 sq mi), Bolivia is the world's 28th-largest country, extending from the Central
Andes through far as the Amazon. The US Geological Service estimates that Bolivia has 5.4 million cubic tonnes of
lithium, which represent 50%–70% of world reserves. (Wikipedia) |
|
|
NEWS HEADLINES - MINING AND METALS |
|
(If blank no updates available this week) |
Purvis Industries acquires Nevada-based distributor
Wed, 02 Jul 2025 17:56:04 +0000
Purvis Industries acquired Johnson Bearing & Supply, a distributor specializing in power transmission products.
<p>The post Purvis Industries acquires Nevada-based distributor first appeared on Pit & Quarry.</p>
Purvis Industries acquired Johnson Bearing & Supply, including all the company’s assets, personnel, brand rights and intellectual property.
Johnson Bearing & Supply is a distributor of power transmission products based in Sparks, Nevada. Purvis says this acquisition strengthens its capabilities in the Western U.S. and enhances the company’s ability to deliver industrial solutions to a broader customer base.
According to Purvis, Johnson Bearing & Supply supports a nationwide customer base, supplying a range of industries including manufacturing, electric motor repair, automotive, medical, high-tech and hobbyist markets. The company specializes in deep groove ball bearings, angular contact bearings, tapered roller bearings, miniature and stainless-steel bearings, spherical bearings, rod ends, bushings, v-belts, shaft collars, O-rings and more.
“We are excited to welcome the Johnson Bearing & Supply team to the Purvis family,” says Jeremiah Johnson, executive vice president & COO of Purvis Industries. “Their expertise, dedication to customer service and strong industry presence complement our values and strategic goals. Together, we will offer enhanced capabilities and value to our customers.”
Glenn Hibl, president of Johnson Bearing & Supply, shares Johnson’s excitement.
“Purvis Industries will enhance the services we can provide to our existing and future customers and create opportunities for our employees,” Hibl says.
Related: Capital Aggregates makes acquisitions in Missouri, Arkansas
<p>The post Purvis Industries acquires Nevada-based distributor first appeared on Pit & Quarry.</p>
|
Limestone trade ticks up in June
Wed, 02 Jul 2025 15:56:04 +0000
Shipments of limestone on the Great Lakes totaled 3.5 million tons in June, up 6.5 percent compared to a year earlier.
<p>The post Limestone trade ticks up in June first appeared on Pit & Quarry.</p>
Limestone shipments on the Great Lakes totaled 3.5 million tons in June, up 6.5 percent year over year.
June’s increase follows a 6.8 percent drop in May reported by the Lake Carriers’ Association (LCA).
According to LCA, June’s loadings were below the month’s five-year average by 1.9 percent. Loadings from U.S. quarries totaled 2.9 million tons, up 12.2 percent compared to a year earlier. Shipments from Canadian quarries totaled 639,301 tons, representing a 13.4 percent year-over-year decline.
Year-to-date, the Great Lakes limestone trade is down 6.5 percent to 9.1 million tons compared to the first six months of 2024. Loadings from Michigan and Ohio quarries decreased 4 percent to 7.5 million tons. Shipments from Ontario quarries total 1.6 million tons, a 16.5 percent decrease in that time frame.
Related: Industry leaders analyze impact of tariffs
<p>The post Limestone trade ticks up in June first appeared on Pit & Quarry.</p>
|
How to solve three common challenges with fine material washers
Wed, 02 Jul 2025 09:00:00 +0000
Dave Schellberg, product support specialist at Eagle Iron Works, presents tips to troubleshoot three common operational issues.
<p>The post How to solve three common challenges with fine material washers first appeared on Pit & Quarry.</p>
Fine material washers are essential components in many aggregate processing operations.
They not only help remove silt and clay from valuable sand, but they play a critical role in ensuring product quality and protecting downstream equipment from unnecessary wear.
Still, like any piece of equipment, fine material washers can experience operational issues that impact performance, efficiency and product specifications. To help producers maintain optimal performance, here are some tips to troubleshoot three of the most common issues encountered in the field, as well as practical solutions to keep screw washers running smoothly.
Before performing any of these maintenance or inspection tasks, be sure to follow all safety protocols. This includes lockout/tagout/tryout before undertaking these tasks.
1. Material buildup in the pool area
One of the most frequently observed issues in fine material washer operations is material accumulating in the washer’s pool area. This can reduce equipment efficiency and increase maintenance requirements if not corrected promptly.
Possible causes & solutions
■ Excessive screw speed. When screw washers operate too quickly, the normal settling pattern of fine particles can be disturbed and allow coarse material to accumulate in the pool.
To resolve this, reduce the screw speed to allow for proper stratification of the material. Running a screen analysis of the feed material can also help determine if the speed settings are appropriate.
For more precise guidance, contact your equipment manufacturer to ensure your screw speed is optimized for your feed gradation.
■ Inadequate silt dilution. If the washer’s overflow appears thick or syrupy, it indicates poor silt dilution. This can lead to excessive buildup.
Flush out the tub with clean water, temporarily cut the feed in half and observe if the issue persists. Increasing the clean water supply to the washer can help thin out the overflow and promote better separation.
■ Washer overload. An overloaded washer can’t properly classify and transport material. Ideally, sand should be seen just spilling over the third exposed screw flight above the waterline. If you notice a heavy buildup, reduce the feed rate to restore balance and avoid unnecessary wear on the screw flights.
Material buildup in the pool area can reduce equipment efficiency and increase maintenance requirements if not promptly corrected. (Photo: EIW)
2. Loss of fines from the washer
Another critical challenge in aggregate processing is the unintended loss of fines from the washer, which can negatively affect product yield and quality.
Possible causes & solutions
■ Too much water in the screen. Excess water can carry fine particles out with the overflow. To determine if fines are being lost, compare a sample of the washed feed against a sample of the final product.
Leveling the weirs and using the overflow depth to calculate gallonage can help you fine-tune the water input. Refer to a hydraulic split chart to understand the optimal water-to-material ratio and adjust accordingly.
■ Inadequate silt dilution. Another way to assess dilution efficiency is by using a hydrometer to measure the specific gravity of the washer water.
A reading above 1.065 suggests excessive silt. If this is the case, flush the washer with clean water, reduce the feed temporarily and rerun a sample analysis to evaluate the extent of fines loss.
3. Discharge too sloppy
A sloppy discharge may signal inefficiencies within the washer that can lead to problems with downstream material handling or product stockpiling.
Possible causes & solutions
■ Drainboard channel plugged. The first thing to check is the drainboard channel. If it’s plugged, water and fines can back up, leading to a slurry-like discharge.
Make sure flush water to the drainboard is turned on and that the trough is clear of any debris or settled material.
Possible causes of a sloppy discharge are a plugged drainboard channel and dirty wash water. (Photo: EIW)
■ Dirty wash water. If the washer is running with muddy or recirculated water full of fines, it will affect the final product. Flush the washer with clean water and temporarily reduce the feed to allow the system to reset. A clearer water stream will result in a firmer, drier sand discharge that’s easier to handle and stack.
Remember …
Like any equipment in an aggregate operation, fine material washers require attention and tuning to ensure they’re operating at peak efficiency.
Many issues – from material buildup to loss of fines – can be traced back to water quality, feed consistency or mechanical settings. Routine inspections and basic sample testing – such as specific gravity or a screen analysis – are essential to diagnose these common problems.
When in doubt, operations can turn to manufacturers who offer field support, diagnostics and equipment recommendations to help operations troubleshoot and fine-tune their systems for better performance and longer equipment life.
By staying proactive with maintenance and understanding the indicative signs of trouble, producers can keep their fine material washers operating efficiently, extend component lifespan and consistently produce a high-quality sand product.
Dave Schellberg is product support specialist at EIW (Eagle Iron Works).
Related: Best operational practices for fine material washers
<p>The post How to solve three common challenges with fine material washers first appeared on Pit & Quarry.</p>
|
Capital Aggregates makes acquisitions in Missouri, Arkansas
Tue, 01 Jul 2025 16:42:02 +0000
The company acquired two Richard J. Mertens operations along with a Dan Processing site.
<p>The post Capital Aggregates makes acquisitions in Missouri, Arkansas first appeared on Pit & Quarry.</p>
Jones
Capital Aggregates acquired two aggregate operations that strengthen its presence in Missouri and Arkansas.
The company acquired the quarry operations of Richard J. Mertens, a Missouri-based business with two quarry sites in the St. Louis area. In a separate deal, Capital Aggregates acquired the sand and gravel operation of Dan Processing, which is located near Batesville in northeast Arkansas.
“These are two highly strategic acquisitions that align with our long-term growth plan,” says Jamie Jones, COO of Capital Aggregates. “The Mertens quarries are a strong geographic fit that allow us to expand our footprint further east in Missouri, while the Batesville-area operation is a great bolt-on addition to our existing sand and gravel and limestone operations in northeast Arkansas.
“Mike Mertens and his sons have built an outstanding business over the years, and we’re excited to welcome them to the Capital Aggregates team,” Jones adds. “Likewise, the Dan Processing site enhances our ability to serve customers more efficiently in a key market where we’re already well established.”
With the acquisitions, Capital Aggregates now operates an expanded portfolio of aggregate sites that supports infrastructure and development projects across Missouri, Arkansas and beyond.
Related: How idler bearing seal tech proves beneficial to Capital Sand
<p>The post Capital Aggregates makes acquisitions in Missouri, Arkansas first appeared on Pit & Quarry.</p>
|
Heidelberg Materials selects new fly ash SVP
Tue, 01 Jul 2025 16:28:33 +0000
Bill Fedorka takes over as Heidelberg Materials’ senior vice president of fly ash in the Southeast following the retirement of Jim Clayton.
<p>The post Heidelberg Materials selects new fly ash SVP first appeared on Pit & Quarry.</p>
Fedorka
Heidelberg Materials named Bill Fedorka senior vice president of fly ash in the Southeast.
Fedorka succeeds Jim Clayton, who is retiring after 20 years at the company.
“Jim’s commitment to building a creative team focused on problem-solving and implementing strategic plans throughout the region has significantly shaped the fly ash industry,” says Scott Dickson, president of the Southeast region at Heidelberg Materials. “His values-driven leadership approach has inspired others and contributed to the company’s long-term sustainability and success.”
Clayton joined The SEFA Group, a predecessor of Heidelberg Materials, in 2005. He served as the director of utility relations until 2011, when he assumed the role of vice president of operations. In 2015, Clayton was promoted to COO, overseeing all plant operations, SEFA transportation, engineering and construction services, business development, safety and environmental matters.
“It has been an honor to work alongside such a talented team,” Clayton says. “I’m proud of what we have accomplished together throughout the years and am excited to see Bill guide our fly ash business into its next phase of growth.”
Over the past two decades, Fedorka has held several leadership positions at The SEFA Group and Heidelberg Materials, including director of engineering and vice president of CCP Services. In his new role, Fedorka will provide technical and strategic direction for fly ash operations and initiatives, focusing on strategic growth, technological innovation and operational excellence.
“I’m honored to take on this new role and continue building on the strong foundation we’ve established in the Southeast,” Fedorka says. “Our team is passionate about innovation and sustainability, and I look forward to driving forward-thinking solutions that benefit our customers, our communities and the environment.”
Related: Heidelberg Materials adds recycling business in Canada
<p>The post Heidelberg Materials selects new fly ash SVP first appeared on Pit & Quarry.</p>
|
Ohio producer discusses first-half 2025 and what’s ahead
Tue, 01 Jul 2025 16:02:35 +0000
Keeney Sand & Stone’s Kevin Keeney shares midyear insights and an outlook for the coming months during an exclusive visit with P&Q.
<p>The post Ohio producer discusses first-half 2025 and what’s ahead first appeared on Pit & Quarry.</p>
Kevin Keeney, the third-generation owner and operator of Keeney Sand & Stone, paid Pit & Quarry a visit at the end of June to reflect on the first half of the year in northeast Ohio and what’s potentially ahead in the coming months.
P&Q: How has 2025 treated Keeney Sand & Stone thus far?
Keeney: I’d say I got spoiled the last four years. We’ve had pretty easy winters in northeast Ohio. My guys were usually back to mining in late February, and it stayed busy.
But this year, we had an old-fashioned winter. It held on longer than usual. The frost held in the ground, and I didn’t start calling guys back until the end of March. Jobs kept getting delayed because of that.
Once we hit April, though, things started moving again. It’s been just as busy as the past several years, and 2025 looks like it’ll be another strong year.
P&Q: Do you expect the work that got pushed aside in the first half of the year to be there for you in the second half of 2025? Also, how important will it be to extend your production season into November or beyond?
Keeney: The projects I knew were coming in 2024 are still on the way. Some are just waiting in the wings. I’m hoping winter holds off until after Christmas, but even if we get through November, we’ll have a solid finish to the year.
My production and jobs might not quite match the last three or four years, but they’ll be close. And that’s only because we had such a slow start to the year.
P&Q: What kind of construction work is keeping Keeney Sand & Stone busy right now?
Keeney: Right now, we’re involved in a lot of big school projects, parking lots and overburden jobs. We’re supplying a large amount of clay fill. New construction’s still strong – especially housing – so we’re doing a tremendous number of driveways and providing materials for a lot of commercial projects.
We haven’t seen much of a slowdown. Like any election year, last year I held off on making some purchases. Our numbers are down a little bit, but it’s strictly weather-related and not anything political.
P&Q: With tariffs and global conflicts making headlines, do you have any long-term concerns for your business or the industry?
Keeney: We use a lot of steel and abrasives, so I wasn’t sure where things were going – especially when it came to screen cloth and the steel we use for fabrication. For a while, it was a bit uncertain.
But things seem to have leveled off. It felt like there was some fear at first, but it hasn’t turned into anything major. Diesel fuel prices are down, and overall, my costs haven’t risen much compared to the past.
Related: Industry leaders share their market views
<p>The post Ohio producer discusses first-half 2025 and what’s ahead first appeared on Pit & Quarry.</p>
|
Report: Policy uncertainty slowing construction demand
Tue, 01 Jul 2025 14:51:53 +0000
The Associated General Contractors of America’s CEO and chief economist offer perspective on the construction market and the need for policy clarity.
<p>The post Report: Policy uncertainty slowing construction demand first appeared on Pit & Quarry.</p>
Leaders at the Associated General Contractors of America (AGC) say construction job growth has stalled in many parts of the U.S. amid growing uncertainty about tax, tariff and labor policy.
To illustrate its point, AGC says construction employment increased in 180 of 360 U.S. metro areas between May 2024 and May 2025.
“Only half of metro areas experienced a year-over-year gain in construction jobs – the fewest since March 2021,” says Ken Simonson, chief economist at AGC. “This appears to support other indications that investors and developers are delaying or canceling planned projects until they know how severely they’ll be affected by evolving tariff and workforce policies.”
AGC says the latest construction spending figures released in early June show construction spending declined over a 12-month period.
“While Washington is working to prevent a massive tax increase, negotiate new trade deals and hopefully boost funding for workforce development, at this point nothing is set in stone,” says Jeffrey Shoaf, CEO of AGC. “The sooner D.C. provides certainty on a host of issues, the more likely construction demand will rebound.”
Related: Industry experts analyze impact of tariffs
<p>The post Report: Policy uncertainty slowing construction demand first appeared on Pit & Quarry.</p>
|
Sandvik debuts next-generation crushers
Tue, 01 Jul 2025 12:59:49 +0000
The company says its newest jaw crushers offer advantages in safety, performance and other areas.
<p>The post Sandvik debuts next-generation crushers first appeared on Pit & Quarry.</p>
Sandvik launched a range of jaw crushers that offers new benefits in safety and performance.
The upgrades include a new hydraulic wedge setting adjustment, a synchronized retraction arrangement, an improved power pack, upgraded guarding and clear, role-based user documentation.
Additionally, Sandvik says its upgraded jaw crushers are manufactured with a welded mainframe and feature material quality improvements.
“Our new upgraded jaw crushers are now more aligned with the full Sandvik range,” says Martin Johansson, global product manager of jaw crushers at Sandvik. “They give our customers even more ability to secure safety, improve productivity and availability, reduce costs and accelerate sustainability with a partner they can count on.”
The jaw crushers are also equipped with Sandvik’s new ACS-j system that simplifies monitoring and control of lubrication, hydraulic settings and eccentric shaft bearing temperature. According to Sandvik, the system’s information is accessible through a web interface that provides customers with easy oversight and control of components and crusher metrics that help maintain optimal performance and availability through easy troubleshooting.
Related: Finlay adds jaw crusher to lineup
<p>The post Sandvik debuts next-generation crushers first appeared on Pit & Quarry.</p>
|
What operators should know about MSHA’s special assessments
Tue, 01 Jul 2025 09:00:00 +0000
Bill Doran and Margo Lopez of Ogletree Deakins explain how routine violations can lead to massive penalties, breaking down how the Mine Safety & Health Administration’s special assessment process works.
<p>The post What operators should know about MSHA’s special assessments first appeared on Pit & Quarry.</p>
We often get calls from operators who are upset about receiving a special assessment from the Mine Safety & Health Administration (MSHA).
In many of these cases, penalties that would normally amount to a small fine under a regular assessment points calculation escalate to tens of thousands of dollars. In many of these situations, figuring out how the special assessment amount was determined can be mystifying.
While we do not necessarily have good answers, MSHA regulations and policy do provide guidance to help you anticipate a special assessment.
Inside MSHA’s process
The regulation at 30 C.F.R. § 100.5 sets out the parameters for the agency’s authority to issue special assessments. It states that MSHA may elect to waive the regular assessment process when conditions warrant.
The regular assessment process is the point system based on the operator’s violation history, the size of the operator, the level of negligence, the effect on the operator’s ability to continue in business, the gravity of the violation and the demonstrated good faith of the operator in abating the violation. The rule requires that those factors also be considered and presented with the special assessment in narrative form, although no explanation regarding the amount of the penalty calculation is required.
MSHA’s Program Policy Manual (PPM) states that special assessments are mandatory for operators when an operator has failed to abate a violation and is receiving daily penalties for that continued failure; a violation is deemed flagrant; and a violation of section 105(c) discrimination protections is made.
With that said, most special assessments arise from the exercise of MSHA’s discretion to issue higher civil penalties in nonmandatory circumstances. According to the PPM, the enforcement circumstances in which MSHA is required to evaluate whether a special assessment is warranted include the following:
■ Regular citations alleging advance notice of inspections; denial of entry to inspectors; and failure to allow authorized miners’ representative to participate in inspection
■ Regular citations alleging a failure to comply with accident scene control orders issued under section 103(j) and (k) of the Mine Act or in conjunction with a pattern notice
■ 104(b) failure to abate orders
■ 104(d) unwarrantable failure orders
■ 104(g)(1) training orders
■ Regular citations issued in conjunction with a 107(a) imminent danger order
■ Violations that contributed to a fatal or serious injury
When one of these types of enforcement actions occur, the inspector is required to complete the Special Assessment Review (SAR) Form (MSHA Form 7000-32). The inspector will include on the form an initial penalty recommendation with a narrative in support. The form is then reviewed by the inspector’s supervisors, who support or oppose the recommendation.
The final decision regarding special assessment is made by the Office of Assessments, Accountability, Special Enforcement & Investigations at MSHA headquarters. This is a wholly internal agency procedure into which operators have no input, because special assessments are usually issued months after any informal conference, and the operator does not know what the inspector has alleged in the SAR form.
A frustrating aspect of this process is that operators generally cannot get access to the completed SAR form. MSHA takes the position – and most judges have agreed – that information in the form is not relevant because the Federal Mine Safety & Health Review Commission assesses penalties de novo and is not bound by MSHA’s proposed penalties. So, what the inspector writes in the SAR form regarding the assessment does not matter regarding the appropriateness of the penalty.
Still, in Consol Mining Co, LLC, Docket No. WEVA 2024-0231 (April 2025), one judge indicated that the SAR might be “marginally relevant” to evaluating MSHA’s high negligence and unwarrantable failure determinations in a case. Nonetheless, that judge still denied access to the SAR because it contained privileged communications of internal agency deliberations.
Final thought
Given this background, it is critical that operators recognize and anticipate when a special assessment might happen. In that circumstance, the operator can directly address the issue in an informal conference and try to have an impact on the subsequent internal agency discussions regarding the issue.
Bill Doran and Margo Lopez are with the national labor, employment and safety law firm Ogletree Deakins. They can be reached at william.doran@ogletree.com and margaret.lopez@ogletree.com.
Related: Ideas for MSHA leaders to consider
<p>The post What operators should know about MSHA’s special assessments first appeared on Pit & Quarry.</p>
|
|
|
|
|
|